Servo drives play a crucial role in modern motion control systems, ensuring precision, speed, and efficiency in automation and robotics applications. Selecting the right servo drive is a critical decision that affects overall system performance, reliability, and cost-effectiveness. A well-matched servo drive optimizes motion control, enhances energy efficiency, and extends the lifespan of machinery.
In this guide, servo drives and controllers manufacturer AMC explores the key factors to consider when selecting a servo drive for high-performance applications, including power requirements, control modes, communication protocols, environmental considerations, and more.
What Is a Servo Drive and How Does It Work?
A servo drive is an electronic device that controls the motion of a servo motor by receiving signals from a motion controller and adjusting the power sent to the motor. It plays a pivotal role in ensuring precise motion control, regulating speed, torque, and position according to application requirements.
Interaction Between Servo Drive, Motor, and Controller
A servo system typically consists of three primary components:
- Servo Motor– Converts electrical signals into mechanical motion.
- Servo Drive– Regulates the power and signals received by the motor.
- Motion Controller– Generates commands based on the required movement profile.
The servo drive interprets control signals from the controller and adjusts voltage and current to the motor accordingly. Feedback from encoders or sensors ensures real-time corrections for accuracy and stability.
What Are the Different Types of Servo Drives?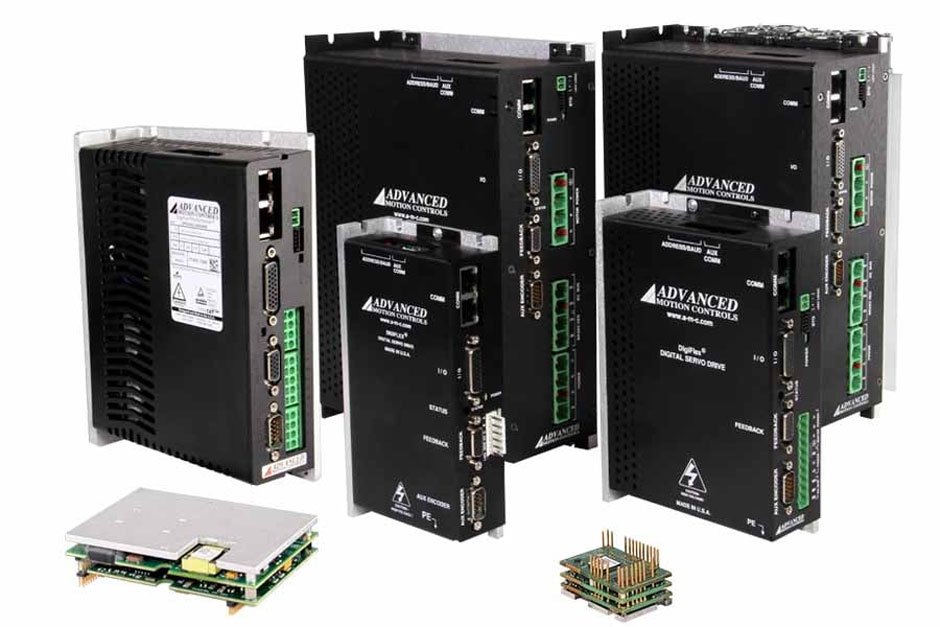
Servo drives come in various types, each suited for different applications based on control requirements, power needs, and system architecture.
Digital vs. Analog Servo Drives
Digital Servo Drives
- Use microprocessors to process control signals with high precision.
- Offer enhanced programmability and diagnostic features.
- Provide better noise immunity and reliability.
Analog Servo Drives
- Use voltage signals to control motor performance.
- Simpler and typically cost-effective for basic applications.
- More susceptible to signal interference compared to digital drives.
AC vs. DC Servo Drives
AC Servo Drives
- Designed for high-speed, high-torque applications.
- Offer smoother performance with better efficiency.
- Commonly used in robotics, CNCmachines, and industrial automation.
DC Servo Drives
- Provide high starting torque and are simpler in design.
- Better suited for low-speed, high-precision applications.
- Often used in applications requiring precise torque control.
Centralized vs. Decentralized Servo Drives
Centralized Servo Drives
- All drives are located in a single control cabinet.
- Easier maintenance and wiring but requires more space.
- Best suited for large-scale industrial systems.
Decentralized Servo Drives
- Drives are distributed closer to motors, reducing wiring complexity.
- Ideal for modular automation systems with space constraints.
- Provides better scalability and flexibility.
What Are the Key Factors to Consider When Selecting a Servo Drive?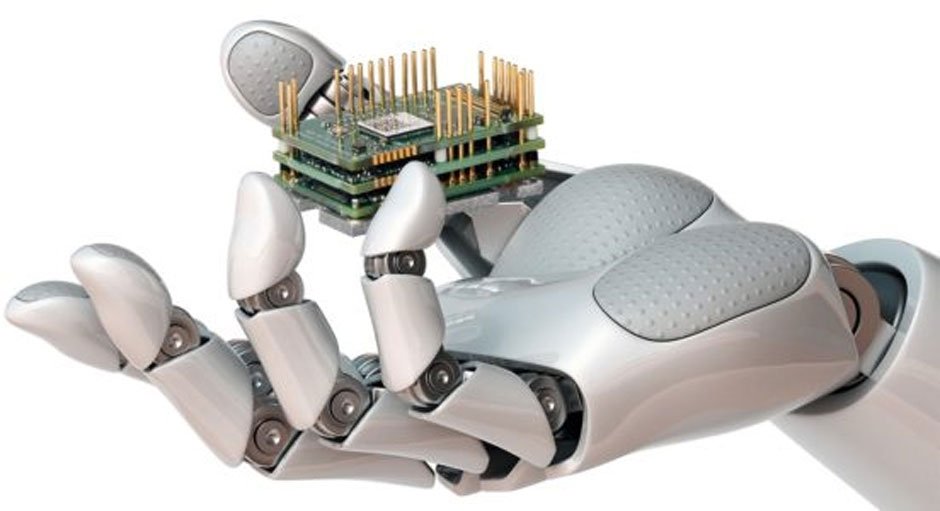
Selecting the right servo drive involves evaluating several factors to ensure compatibility and optimal performance.
Key Selection Criteria:
- Power and voltage ratings
- Torque and speed requirements
- Communication protocols
- Feedback and encoder compatibility
- Control modes
- Environmental and operational considerations
- Safety features
- Sizing and load characteristics
Each of these aspects significantly impacts the efficiency and reliability of the servo system.
What Safety Features Should You Look for in a Servo Drive?
Servo drives must include essential safety mechanisms to protect both equipment and personnel.
- Safe Torque Off (STO):Prevents unexpected motor activation.
- Safe Motion Functions:Enables controlled stopping and emergency braking.
- Overload and Short-Circuit Protection:Prevents damage due to electrical faults.
- Thermal Protection:Monitors and regulates temperature to prevent overheating.
How to Properly Size a Servo Drive for Your Application?
Sizing a servo drive correctly ensures optimal performance and longevity.
Key Parameters for Drive Sizing:
- Load inertia
- Acceleration and deceleration requirements
- Duty cycle
- Mechanical system constraints
Step-by-Step Guide on Calculating Drive Size:
- Identify motor torque and speed requirements.
- Calculate load inertia and compare it with motor capabilities.
- Determine power supply compatibility.
- Consider application-specific requirements such as environmental factors.
What Are the Most Common Mistakes When Choosing a Servo Drive?
Avoiding common pitfalls can save time and resources.
- Undersizing or oversizing the servo drive
- Ignoring power supply compatibility
- Overlooking feedback resolution
- Choosing the wrong communication protocol
What Are the Advantages of Using a Servo Drive Over Other Motion Control Methods?
Servo drives offer several benefits over traditional motion control technologies.
- Higher precision and accuracy
- Greater efficiency
- Flexibility and programmability
- Energy savings
How to Set Up and Configure a Servo Drive?
Proper setup ensures smooth operation and optimal performance.
Setup Steps:
- Wiring and Connection:Ensure correct cabling and secure connections.
- Configuring Control Parameters:Adjust settings to match application needs.
- Tuning the Servo Drive:Optimize performance through parameter adjustments.
What Are the Best Practices for Servo Drive Tuning?
Tuning a servo drive enhances system stability and efficiency.
- Adjust PID gains to optimize response times.
- Use auto-tuning features if available.
- Monitor system behavior and make fine adjustments as needed.
What Are the Best Maintenance Practices for Servo Drives?
Regular maintenance extends the lifespan and reliability of servo drives.
- Routine inspections to detect wear or damage.
- Troubleshooting common faults promptly.
- Perform firmware and software updates when necessary.
What Are the Best Servo Drives on the Market?
Selecting a high-quality servo drive depends on several factors.
Selection Criteria:
- Performance specs
- Compatibility with industry standards
- Manufacturer reputation
- Cost vs. performance trade-offs
What Are Alternative Motion Control Technologies to Servo Drives?
While servo drives offer high precision, alternatives may be suitable for different applications.
Alternative Solutions:
- Stepper Motors– Simple and cost-effective for basic positioning.
- Variable Frequency Drives (VFDs)– Efficient for speed control applications.
- Hydraulic and Pneumatic Actuators– Ideal for high-force applications.
- Linear Motors– Used in applications requiring direct linear motion.
Conclusion
Selecting the right servo drive is crucial for achieving high-performance motion control. By considering factors such as power requirements, control modes, communication protocols, and environmental conditions, engineers can optimize system efficiency and reliability. Understanding the advantages and potential pitfalls of different servo drive technologies ensures informed decision-making for any motion control application.